What is Porosity in Welding: Necessary Tips for Getting Flawless Welds
Wiki Article
Porosity in Welding: Identifying Common Issues and Implementing Best Practices for Prevention
Porosity in welding is a prevalent problem that often goes unnoticed till it causes substantial issues with the integrity of welds. In this discussion, we will certainly explore the crucial variables contributing to porosity development, analyze its damaging effects on weld efficiency, and discuss the finest techniques that can be embraced to lessen porosity occurrence in welding procedures.Common Root Causes Of Porosity

Another regular culprit behind porosity is the presence of contaminants on the surface of the base metal, such as oil, oil, or rust. When these pollutants are not successfully gotten rid of prior to welding, they can evaporate and come to be entraped in the weld, causing flaws. Moreover, utilizing unclean or wet filler materials can present pollutants into the weld, adding to porosity issues. To minimize these usual sources of porosity, comprehensive cleansing of base metals, appropriate shielding gas selection, and adherence to ideal welding parameters are necessary methods in attaining top quality, porosity-free welds.
Effect of Porosity on Weld Top Quality

The existence of porosity in welding can substantially jeopardize the structural integrity and mechanical residential or commercial properties of bonded joints. Porosity creates voids within the weld metal, damaging its overall strength and load-bearing ability. These gaps act as stress focus points, making the weld extra at risk to fracturing and failing under used lots. Furthermore, porosity can reduce the weld's resistance to rust and various other ecological factors, even more decreasing its long life and efficiency.
Among the key effects of porosity is a reduction in the weld's ductility and strength. Welds with high porosity levels have a tendency to exhibit reduced effect stamina and minimized capacity to flaw plastically prior to fracturing. This can be especially concerning in applications where the welded elements go through vibrant or cyclic loading problems. Porosity can impede the weld's capacity to effectively send pressures, leading to early weld failing and potential safety threats in essential frameworks. What is Porosity.
Best Practices for Porosity Prevention
To boost the structural integrity and high quality of welded joints, what details procedures can be applied to lessen the occurrence of porosity during the welding process? Making use of the right welding technique for the details product being welded, such as changing the welding angle and gun setting, can further stop porosity. Regular evaluation of welds and instant removal of any kind of problems recognized throughout the welding process are necessary methods to stop porosity and produce top quality welds.Significance of Correct Welding Methods
Executing correct welding strategies is paramount in guaranteeing the structural honesty and quality of welded joints, constructing upon the foundation of efficient porosity prevention actions. Excessive warmth can lead to enhanced porosity due to the entrapment of gases in the weld pool. Additionally, using the ideal welding criteria, such as voltage, current, and travel more helpful hints rate, is important for attaining sound welds with marginal porosity.Additionally, the choice of welding procedure, whether it be MIG, TIG, or stick welding, should straighten with the certain requirements of the job to guarantee optimal results. Appropriate cleaning and preparation of the base steel, as well as selecting the best filler material, are also important parts of efficient welding techniques. By sticking to these best practices, welders can lessen the risk of porosity development and create top notch, structurally sound welds.
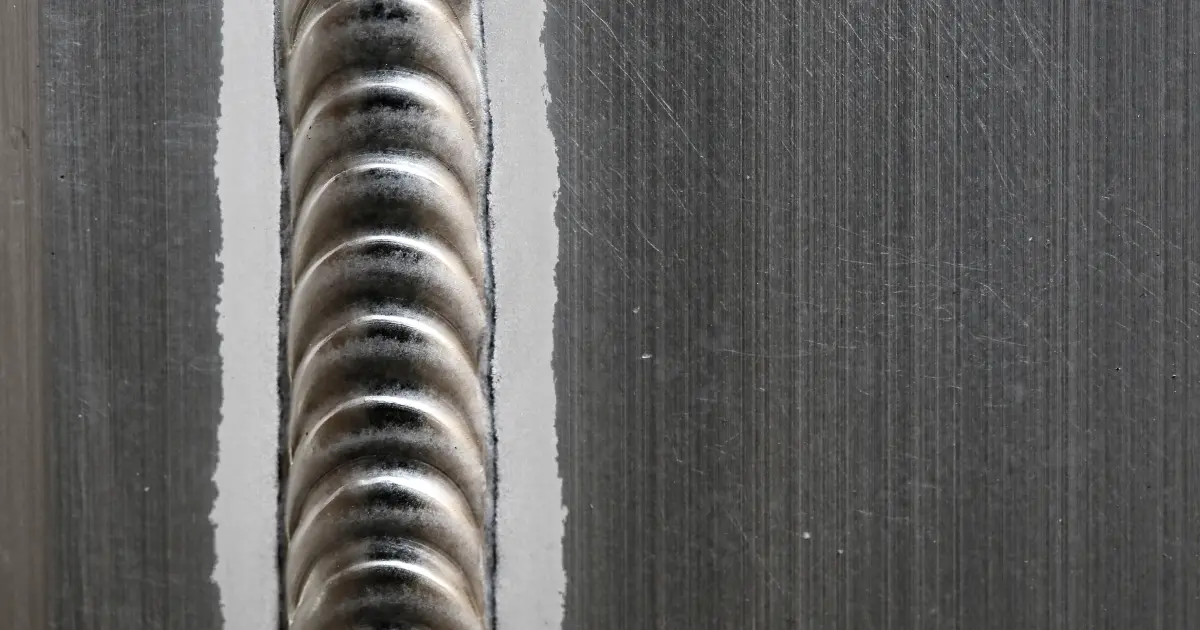
Examining and Quality Assurance Procedures
Checking procedures are vital to detect and avoid porosity in welding, making certain the strength and durability of you can try this out the final product. Non-destructive testing approaches such as ultrasonic screening, radiographic screening, and visual assessment are generally employed to identify potential flaws like porosity.Post-weld examinations, on the various other hand, assess the last weld for any kind of flaws, including porosity, and validate that it satisfies defined standards. Implementing a thorough top quality control plan that includes comprehensive testing procedures and assessments is vital to decreasing porosity issues and making certain the general quality of bonded joints.
Verdict
Finally, porosity in welding can see this website be an usual issue that affects the top quality of welds. By identifying the typical reasons of porosity and applying finest practices for avoidance, such as correct welding techniques and screening procedures, welders can ensure premium quality and trustworthy welds. It is important to focus on avoidance techniques to lessen the occurrence of porosity and maintain the honesty of bonded frameworks.Report this wiki page